Leichte, modulare Elektroautos für die Stadt
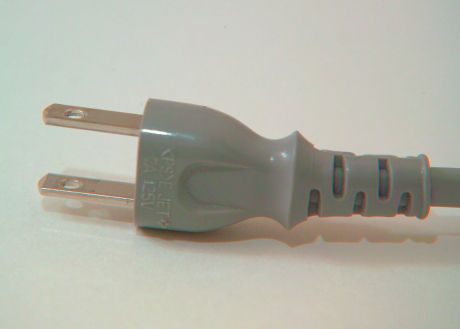
JapanesePlug
By No machine-readable author provided. Fg2 assumed (based on copyright claims). [Public domain], via Wikimedia Commons
Danke der Entwicklung innovativer Rohkarosserien mit Hilfe von leichten Aluminium- und Verbundwerkstoffen sind Elektrofahrzeuge näher an die Realität herangerückt.
EVOLUTION (The Electric Vehicle revOLUTION enabled by advanced materials
highly hybridized into lightweight components for easy integration and
dismantling providing a reduced life cycle cost logic) verwendet das
Konzeptfahrzeug von Pininfarina Nido als Referenz für seine Aktivitäten.
Das bestehende Konzept der Rohkarosserie wurde durch eine
Design-Strategie komplette überarbeitet, um die Anzahl der Teile zu
reduzieren und den Einsatz innovativer Leichtbaumaterialien zu
überprüfen.
Der ausgewählte Karosserieurtyp mit einer zentralen Zelle ist angesichts des Montageprozesses konsolidierter Standard, um leicht von einem niedrigen zu einem hohen Produktionsvolumen umschalten zu können. Grundsätzlich hat die Zelle eine strukturelle Funktion, während das Vorderteil so dimensioniert ist, dass es Energie während eines Frontalaufpralls absorbieren kann und das hintere Ende modular aufgebaut ist, so dass in Transporter und Pick-up-Versionen umgewandelt werden kann.
Die Al-Technologien, die auf Al 5xxx-6xxx und 7xxx-Legierungen angewandt werden, bieten die Möglichkeit, Teile mit komplizierten Geometrien und geringer Dicke zu erhalten, und verschiedene Teile in einem einzigen Element zusammenzuführen. Außerdem ist es möglich, ein Element mit einer einzigen Operation und variablen Dicken zu verarbeiten.
Eine "grüne Sandform"-Technik ermöglicht es, gemischt-gegossene Fugen zwischen verschiedenen Elementen mit verschiedenen Fertigungsverfahren zu erhalten.
Die potenzielle Kostenreduzierung und Prozessvereinfachung im Hinblick auf Zeit und Montage sind vielversprechend: der aktuelle Stand der Technik auf der Basis traditioneller Gussformen hat diese Möglichkeiten nicht zugelassen.
Die Rohkarosserie wurde in bestimmten Bereichen des Unterbodens mit einem mit GF verstärkten Verbundmaterial aus der PA-Familie hybridisiert. Dieses Material wurde durch die Verbesserung bestehender Materialien und die Entwicklung eines Produktionsprozesses gewonnen, um dieses auf kommerzielle Anforderungen über fortgeschrittenes Platten-Thermoformen und 3D-Injektionsverfahren (CaproCAST Prozess)hin zu skalieren.
Neuartige Polypropylen Nanokomposite (polypropylene nancocomposites, PNC), die auf Schichten von Silikaten und Glasfasern basieren, weisen eine verbesserte Zähigkeit und Steifigkeit auf und wurden für Crash-Querträger und Seitentür-Demonstratoren ausgewählt. Polyurethanschaumstoffe auf Basis von Recycling-Polymeren werden für die Verwendung als nachhaltige Energieabsorptionsfüllung in Querträgerabschnitten untersucht.
Struktur Epoxidklebstoffe wurden berücksichtigt, um die BiW-Teile zusammenzuführen und die Anzahl der Schweißstellen zu reduzieren: Punktschweißungen wurden in bestimmten Bereichen ausschließlich dazu verwendet, um die Teile während der Polymerisation aneinander zu heften.
Neben den vorherigen Ergebnissen, beträgt das aktuelle Gewicht der Rohkarosserie 115 kg gegenüber 160 kg des Fahrzeugs der Basislinie. Eine FE-Analyse über das virtuelle Gesamtfahrzeug legt als Belege über ein gutes Tragverhalten vor, wenn man die Homologierung der EU Crashstandards und globale statische und dynamische Leistungen berücksichtigt.
Die innovative Architektur und die Integration von leichten Materialien sorgen dafür, dass die EU ihre Wettbewerbsfähigkeit gegenüber der asiatischen und US-amerikanischen Automobilindustrie beibehält.
veröffentlicht: 2015-11-23