Intelligente Miniaturgeräte aus Kunststoff
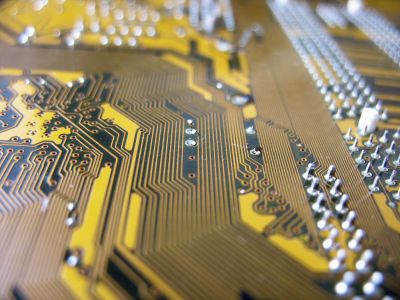
Smart miniaturized plastic devices
Spritzgegossene Schaltungsträger (Moulded Interconnected Devices, MIDs) weisen alle Eigenschaften spritzgegossener Kunststoffteile auf und verfügen zugleich über integrierte Leiterbahnen und elektronische Komponenten.
Das Konzept der 3D-MIDs besteht seit den 1980er-Jahren. Obwohl die Technologie große Vorteile gegenüber herkömmlichen gedruckten Schaltkreisen verspricht, standen verschiedene Probleme ihrer industriellen Anwendung bislang im Wege. Doch da die Technologie immer weiter ausreift, könnte sie bald den komplexen und kostenintensiven Anforderungen, die an sie gestellt werden, gerecht werden.
Der jährliche Marktzuwachs lag über einen Zeitraum von mehreren Jahren konstant bei etwa 20 %, und europäische Wissenschaftler möchten die Marktpräsenz mithilfe des EU-geförderten Projekts "Pilot factory for 3D high precision MID assemblies" (3D-HIPMAS) weiter erhöhen. Die Technologie wird in einer futuristischen europäischen Pilotfabrik präsentiert werden. Vier Demonstrationssysteme sind geplant – für eine Mikrobrennstoffzelle, ein Hörgerät, einen Mikroschalter und einen Drucksensor für den Einsatz in der Automobilbranche.
Zur Herstellung wird Kunststoff mittels Laser-Direkt-Strukturierung (LDS) selektiv plattiert. Dabei "zeichnet" ein Laserstrahl einen Schaltkreis auf die Oberfläche eines mit einem lasersensitiven Zusatzstoff versetzten Kunststoffteils. Die Oberfläche des aktivierten Kunststoffs wird dann mit Metallschichten plattiert, wie sie in ähnlicher Form auch bei gedruckten Leiterplatten zu finden sind.
Die Wissenschaftler wählten Kunststoffrohmaterialien aus und entwickelten mehrere neue, hochleistungsfähige, mit neuen feinkörnigen LDS-Zusatzstoffen versetzte Thermoplaste. Ebenso entwickelten sie eine Lasermaschine mit sehr präzisem Fokus sowie ein neues Plattierverfahren zur Herstellung feinster Leiterbahnen mit einem Durchmesser von bis zu 70 µm.
Beim Zweikomponentenspritzguss, dem etablierteren Verfahren, werden Polymerharze in zweistufigem Spritzguss gegossen, anschließend aktiviert und somit für das sich der Leitfähigkeit bedienende Plattierverfahren vorbereitet. Auch das innovative experimentelle Zweikomponentenspritzgussverfahren wurde ausgebaut und wird derzeit weiter optimiert.
Die Forscher arbeiten derzeit auch an der richtigen Anordnung der 3D-Präzisionselektronikkomponenten sowie an der Entwicklung verlässlicher Überwachungs- und Qualitätssicherungsverfahren. Es wurden Konzepte zur dreidimensionalen Anordnung und Formung entwickelt, welche einen hohen Grad an Präzision und hohe Durchsatzraten ermöglichen. Derzeit arbeitet das Forschungsteam an der Erstellung eines Röntgeninspektionssystems, welches zur Online-Prozess- und -Qualitätssicherung eingesetzt werden soll.
Die im Rahmen des HIPMAS-Projekts entwickelte 3D-Technologie verspricht einen reduzierten Rohmaterial- und Energieverbrauch sowie verbesserte Zykluszeiten und höhere Produktionserträge. Ein Plan zur Eingliederung einzelner Bausteine in industrielle Produktionsanlagen in ganz Europa wurde bereits ausgearbeitet. So soll Europa bei der Herstellung intelligenter Kunststoff-Mikrokomponenten wettbewerbsfähiger werden.
veröffentlicht: 2015-04-22